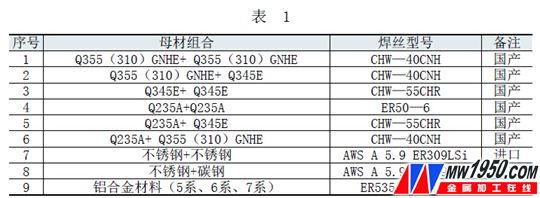
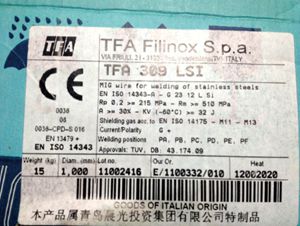
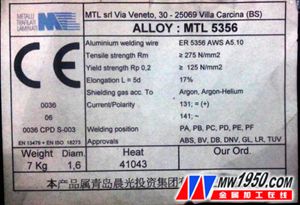
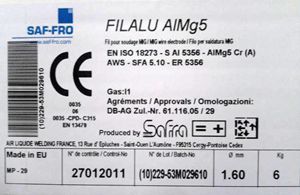
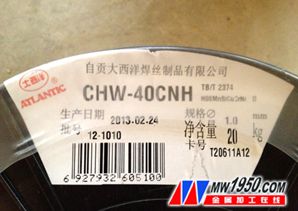
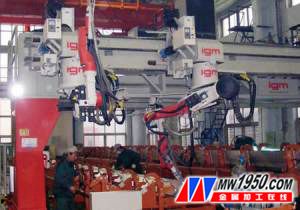
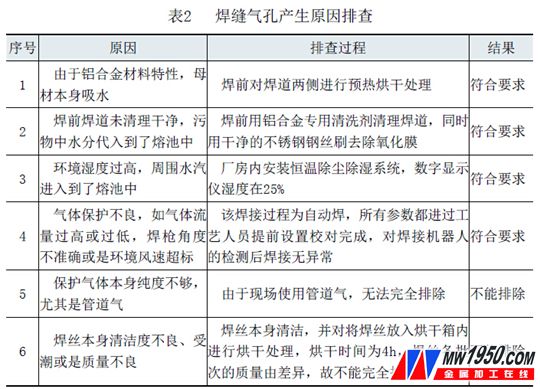
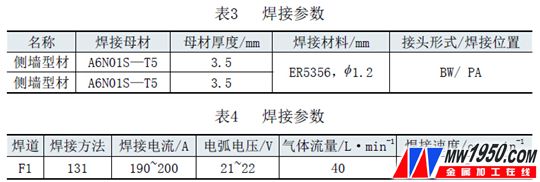
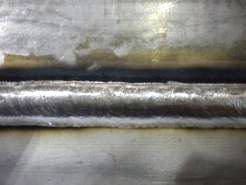
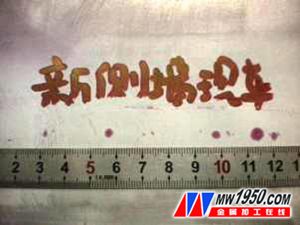
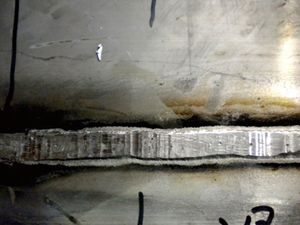
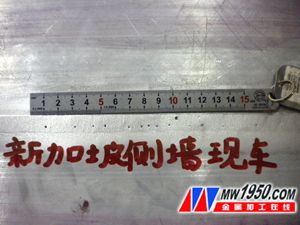
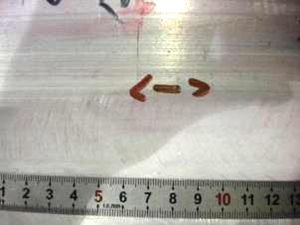
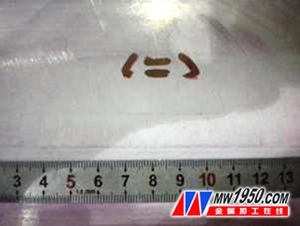
(a) Test 1: No. 2 welding wire + pipe gas result: weld defect after PT flaw detection (b) Test 2: No. 2 wire + bottled gas result: weld defect without defect after PT flaw detection   Â
(c) Test 3: No. 1 welding wire + bottled gas result: Porosity defect in weld after PT flaw detection  (d) Test 4: No. 1 welding wire + pipe gas result: Pore defect in weld after PT flaw detection Â
Figure 4 Â Â Â Â Â Â Â Â Â Â Â Â Â Â Â Â Â Â Â
household stove burner,gas stove bottom burner,Gas Cooker Burner,gasstove burner
GUOLONG PRECISION VALVE CO.,LTD , https://www.glstovevalve.com