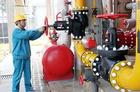
In order to change the backwardness of China's chemical safety management, the State Administration of Work Safety and Dow Chemical cooperated to launch the first phase of hazardous chemicals safety management demonstration cooperation project in 2006, and the end of 2008. In the past three years, Dow Chemical has delivered more than 50 chlor-alkali and ** enterprises in 17 provinces and cities in China, delivering advanced safety management technologies and experience. In 2011, the two parties once again joined hands to initiate the second phase of the project cooperation for two years. They chose Hangzhou Dianhua, Jiangsu Thorpe, and Shandong Lihuayi to become pilot projects that are “small, precise, and detailedâ€. Hanghua Power is the only domestic pilot company that has participated in two phases.
He Baichuan, vice president of Dow Chemicals responsible for manufacturing operations and public and government affairs in the Asia-Pacific region, said: “Through joint cooperation, we will help companies in the industry to train safety-related personnel based on their respective local conditions and conditions, gradually establish standardized processes and establish a crisis. Chemicals management system. It is understood that in the second phase of the project, Dow Chemical sent a technical team led by EHS directors from the Asia Pacific region and China to guide the staff of Hangzhou Electrochemical to electrolysis, chlorine and hydrogen, and other processes. Process testing. On the basis of listening to expert advice, Hangzhou Dianhua changed the design of the original process, equipment, and instrumentation system. As far as possible, no seams were used on the production device to reduce the sealing points when connecting the equipment.
During the visit to Hangzhou Electrification Site, the reporter saw that in the vertical storage tank area where the storage tank was stored, the sampling port of each tank was designed as a funnel with a lid, and the pipeline was laid below. If the sample leaked out, the liquid would Follow the inflow and then concentrate on recycling. The company’s Assistant Minister of Production said: “This small innovation was learned from Dow.â€
In the implementation of the second phase of the project, the Chemical Registration Center under the State Administration of Work Safety assisted Hanghuan to carry out process hazard analysis, conducted hazard and operability analysis (HAZOP) and protective layer analysis (LOPA), and established equipment. Leak detection technology and management system.
Huang Yezhao, chairman of Hanghua Power, introduced: “Our company has a 76-year history, the original foundation is behind, and the level of safety management is poor; through the implementation of the two-phase cooperation project and careful study of Dow's philosophy and experience, we insist on grasping the essence. Grasping the standards and grasping the basics, the quality of the safety management system continued to improve, and the safety environment continued to improve.Compared with the two years prior to the pilot project, the frequency of accidents decreased significantly during the six years after the trial, and the accident coefficient dropped from 3.02 in 2005 to this year. 0.08;In February of this year, the company passed the acceptance of the national second-level safety standardization enterprise, and was rated as the Top Ten Enterprise for Corporate Social Responsibility Construction in Hangzhou.The next step is to create a standardized first-tier enterprise and achieve zero harm. Zero accident, the highest goal of zero pollution."
Regarding the issue of safety production in high-risk industries such as chlor-alkali that people are concerned about, Sun Huashan emphasized that scientific planning, rational distribution of high-risk chemical companies, and improvement of access thresholds and strict approvals should be followed. The project site selection must be consistent with the overall land use planning and related Standard requirements, deepen special rectification, eliminate backwardness, do a good job of shutting down or relocating chlor-alkali enterprises outside the park, realizing withdrawal from the city into the park; improve the intrinsic safety level of chlor-alkali and other high-risk enterprises' processes and equipment, and their production facilities must implement automatic control and For on-line testing, safety interlocks, emergency stop systems, automatic leak monitoring facilities, and automatic absorption devices for highly toxic gas leaks should be set up to raise the level of intrinsic safety at the source and safeguard the lives and property of the general public.
Sun Huashan said: "The existing chlor-alkali enterprises must reach the second-level or higher level of safety production standardization before the end of 2015; the newly-built enterprises will achieve the safety-production standardization level of two or more levels within three years after obtaining a safety production license."
The injection molding process has revolutionized the medical device industry. The manufacture of medical devices through injection molding allows companies to products that are lightweight and cost-effective, and allows for more expedient completion of those products.
When it comes to the manufacturing of medical devices, top-level care must be given to every aspect of the process that creates these vital medical instruments. Clients and patients alike depend on products that deliver uncompromised quality and consistency.
Our commitment to top grade development standards gives clients the assurance that the highest quality products and top level commitment to service excellence are a part of every order. Providien has the capability to manufacture medical devices in several capacities.
Medical Injection Mold,Mould For Medical Use,Medical Syringe Plastic,Container Plastic Injection Mould
PF Mold Co., Ltd. , http://www.pf-mold.com