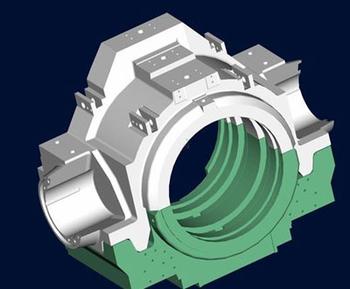
2. Scope of application: These rules apply to the use and management of the molds required by the company's production units to carry out production activities.
Operation specification 3. Before hanging the mold, it is necessary to wipe the dirt on the mold plate before and after the mold and the mold to be cleaned.
4, for the single-sided core-pulling mold, when installing the mold, should pay attention to the position of the core, single-sided core-pulling mold, generally with the core block to the rear security door direction device mold; double-sided core-pulling mold, generally using the core Block front and rear safety door direction device mold.
5. During the mold adjustment process, the crankshaft of the machine must be straightened, the mold should be properly tightened, and the mold should be adjusted with a speed and pressure of 20% or less until it can not be mobilized. Immediately release the mold adjustment key and fix the mold. After firm, open the mold and adjust it properly.
6. When connecting the cooling water, it is necessary to close the mold first, and it is forbidden to collide the slider or operate in an irregular manner.
7, adjust the machine thimble, the stroke should be adjusted to just eject the product is appropriate, not to top out too long to prevent damage to the mold.
8. For molds whose thimble needs spring return, all microswitches or mechanical protection devices must be connected to ensure that the thimble can be safely reset; during production, the thimble is prohibited from closed mold production without complete reset.
9. When commissioning the product, injection molding should be started with 30% of the pressure and speed, and the pressure and speed should be gradually increased. Before any mold enters normal production, it must be adjusted to the low pressure protection setting type.
10. When the mold reaches a certain mold temperature (usually 30 molds after normal production), the cooling water is turned on; if the mold has been preheated to the working temperature before production, the cooling water can be directly opened.
11, when the next die, you should turn off the cooling water, and then produce 3-5 minutes, wipe the cavity with a clean rag, coated with oil or rust inhibitor, do a good job of protection against rust.
12. The molds changed from the machine table, the gates are not allowed to face downwards, and they are preferably placed upwards in the mold placement area.
13. When the preheating is performed, it is necessary to retract the ejector pin in the mold (do not close it too tightly); perform even heating and avoid point heating, which will easily cause the mold to anneal.
14. In the case of non-clamping, it is forbidden for the machine to advance against the front mold so as not to loosen or knock away the front mold.
Abnormal situation processing 15. During the operation process, the operator must ensure that there are no leftovers in the mold before each mold product is produced.
16, found in the operation of sticking mold, the product should be removed before the mold production, no mold cavity with the production of materials.
17. After die-bonding, the die cavity should not be knocked with iron. The special copper rod should be used to pull out the product. The correct method is to stick the copper rod to the die surface and pull out the product (It is forbidden to use the parting surface of the die as the fulcrum to carry the product. ).
18. In the course of operation, if there is a deep-caved sticky material, disabling the metal object knocking (the correct method is to insert the iron wire into the plugging position after the red wire is burned, and then pull out after cooling to bring out the sticky aluminum material).
19. During the operation, the pin on the mold, the movable slider and the ejector pin should always be lubricated and lubricated (the more the clamping pressure is, the more frequent the refueling is. Normally, it is added once every 8 hours. After joining, it will twitch several times to prevent burns from being stuck. ).
20. During the operation process, it is forbidden to use pliers to clamp the material head when it is found that the material head sticks to the front mold to prevent excessive force from damaging the mold cavity (the correct method is to withdraw the machine platform and use a copper rod from the sprue bushing Knock out the material head.
The molds are kept in use 21, molds that are not used for production are placed neatly on the mold base by number;
22. After the batch is finished, the mold should be inspected and confirmed immediately. If the mold is normal, it will be stored in the warehouse. If the mold is abnormal, it will be repaired immediately. For the mold to be repaired, the workshop supervisor will fill in the “repair list for the equipmentâ€. After the manager approves, the mold will be repaired. , It is forbidden to ship without delivery.
23. When handling molds, special care should be taken to ensure that the molds are placed in a stable position during transportation; when the molds are lifted and removed with a lift truck before the mold stands, the parking spaces should be fixed before the lifting work can be performed. The fork must be placed at a minimum during transport to prevent it from falling.
24. In order to prolong the service life of the mold and prevent premature cracking of the mold, quenching and tempering should be performed when the mold is used up to 3000 molds, 10,000 molds, and 40,000 molds.
25. Dies that have been damaged due to die damage are inspected by the workshop supervisor and reviewed by the Engineering Department, and are divided into three stages according to scrapping, partial scrapping, and repairing.
Accident responsibilities and punitive measures 26. Any damage to the mold shall be reported to the casting supervisor at the first time, and the party shall be held accountable according to the circumstances.
27. If it is discovered that it has not taken the initiative to declare a mold failure, the on-duty operator and its on-duty personnel will share their responsibility.
28. Serious penalties are imposed on those who knowingly committing or evading responsibility, and those who are severely dismissed.
29. These Rules shall be implemented as of the date of promulgation.
Stainless Steel Sanitary Tubing is the main tubing line for a piping system. Generally, sanitary welded tubings are made in stainless steel 304 and 316l, but we provide other grade too such as hastelloy C22, 316Ti, Titanium and nickel alloy etc. Kaysen offer both Sanitary Seamless Tubes and Sanitary Welded Tubes to ASTM A270, ASTM A249, A269, ASTM A554, DIN11850, and size is up to 12″. Inner and outer surface is polished to meet the high purity requirement of hygienic industries. Kaysen sanitary is ability to supplying qualified sanitary tubings comply to your your condition and FDA,GMP requirement.
Stainless Steel Sanitary Welded Tubing-Sanitary Tubing
Material: SS304, SS316L, EN 1.4301, EN 1.4404, etc
OD diameter: 1/2" - 12"
Thickness: 0.5mm - 6mm
Standard: ASTM, JIS, DIN, JIS, SUS, GB
Length: 6m or customer made
Tolerance: OD. ±0.2mm; Thickness: ±0.02mm; Length: ±0.5mm
Surface Treatment: Matt Finish or Mirror Finish (320# 400# 600#) etc
Application: Boiler, heat exchanger, construction, hygienic, pharmacy, power, petrochemical
Strength:
Heat Treatment of solution annealing for the sanitary tubings and fittings are available
High precision on dimension and wall thickness
Both seamless and welded sanitary tubings are available
Length is up to 12 meters.
Min. order quantity of sanitary tubings is from 300Kgs.
Offer industrial pipe and tubes according to order.
PMI test to verify material grade.
Visual and surface 100% examination before shipment.
End protected for shipment.
Sanitary Welded Tubes
Sanitary Welded Tubes,Sanitary Tubes ,Stainless Steel Sanitary Tubes,Stainless Steel Welded Pipes
Kaysen Steel Industry Co., Ltd. , http://www.chinasanitaryvalve.com